Hype oder aufkommende Notwendigkeit: Ist virtuelle Inbetriebnahme am digitalen Zwilling sinnvoll?
Bringen die neuen Modebegriffe rundum die virtuelle Inbetriebnahme an digitalen Zwillingen wirklich einen Benefit in der Steuerungstechnik oder handelt es sich hierbei nur um einen temporären Hype? Kann die Qualität der Steuerungssoftware ohne wesentlichen Mehraufwand gesteigert werden? Wird mit Hilfe der virtuellen Inbetriebnahme wirklich Zeit eingespart?
Das sind berechtigte Fragen, mit welchen sich jeder Entscheidungsträger auseinandersetzen muss, der sich mit dieser aufkommenden Technologie beschäftigt. In diesem Beitrag werde ich auf diese Kernpunkte eingehen und das Mysterium rundum dieses neuartige Engineering-Werkzeug lüften.
Mit ungetesteter und fehlerhafter Steuerungssoftware zur Inbetriebnahme
Welcher Steuerungstechniker kennt es nicht? Immer weniger Zeit zur Programmierung, doch zunehmend größere und komplexere Maschinen mit anspruchsvollen wachsenden Zusatzfunktionen. Doch die Vorgehensweise ist seit Jahren dieselbe. Ein provisorisches Steuerungsprogramm entsteht durch den Programmierer parallel zum Herstellungsprozess (Beschaffung, Zusammenbau und Verkabelung der Maschine) und soll innerhalb von einem kurzen Zeitfenster auf der Baustelle beim Kunden in Betrieb genommen werden.
Das „provisorische Steuerungsprogramm“, das zum Zeitpunkt des Inbetriebnahme-Starts an der realen Maschine vorliegt, kann im Vorfeld nur sehr rudimentär getestet werden. Ganzheitliches Testen, also das Zusammenspiel aller Steuerungsebenen, aller Maschinenbereiche und dessen externen Abhängigkeiten, muss unter Zeitdruck an der realen Maschine beim Kunden durchgeführt werden.
Die ersten Fehler und Bugs in der Software, die während der Inbetriebnahme nicht aufgetreten sind, machen sich spätestens während des laufenden Produktionsprozesses nach Abschluss bemerkbar, da in den meisten Fällen nicht alle Szenarien gründlich und vollständig, vor allem im Dauerbetrieb, getestet werden konnten.
Im einfachsten Fall führt das im Nachgang zu kostspieligen Serviceeinsätzen, während die ganze Produktion stillsteht. In anderen Fällen kann fehlerhafte Software auch zu erheblichen mechanischen Schäden führen, wenn beispielsweise ein Roboter aufgrund eines Kommunikationsfehlers die falschen Zielkoordinaten erhält.
Um Abhilfe von fehlerhafter Software und stressigen Inbetriebnahmen beim Kunden zu schaffen, soll die Steuerungssoftware bereits parallel zur Entstehung an der digitalen Maschine getestet und auch virtuell in Betrieb genommen werden.
Die Firma Eberle Automatische Systeme nutzt dafür seit einigen Jahren die Simulationssoftware twin von digifai, um ihre Sondermaschinen bereits vor der realen Inbetriebnahme vollständig zu testen und in Betrieb zu nehmen.
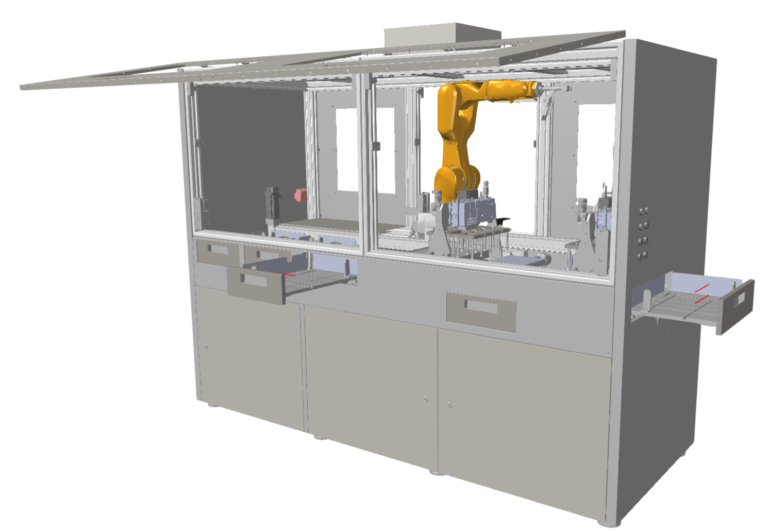
Abbildung 1: Die 3D-CAD-Daten der zukünftigen Produktionsmaschine werden als digitaler Zwilling mit twin abgebildet.
Ganzheitliches Testen von Software am digitalen Zwilling mit virtueller Inbetriebnahme
Eberle nutzt das Werkzeug rundum die digitalen Zwillinge, um sich einen Wettbewerbsvorteil gegenüber der Konkurrenz zu schaffen. Angefangen mit den ersten CAD-Skizzen einer Anlage, führt Eberle mit twin Machbarkeitsstudien (siehe Beitrag hier) durch, um valide, aussagekräftige und vor allem seriöse Angebote für Kunden in der Angebotsphase Vorverkaufsphase erstellen zu können.
Ist das Projekt verkauft, wird die Maschine anhand der konstruierten 3D-CAD-Daten als digitaler Zwilling mit twin, wie in Abbildung 1 ersichtlich, nachgebildet. Die Simulationssoftware bietet dazu eine umfangreiche Bibliothek mit Simulationskomponenten an, mit welchen die Maschine anhand weniger Handgriffe „zum Leben erweckt“ wird.
Um nun Steuerungssoftware schreiben und parallel dazu ganzheitlich testen zu können, wird die virtuelle Maschine an die notwendigen Steuerungen angebunden, wie in Abbildung 2 dargestellt wird. Die nachgebildete, digitale Maschine besteht aus der exakt gleichen Aktorik und Sensorik, wie das reale Pendant. Dadurch erkennen die angebundenen Steuerungssysteme keinen Unterschied zur realen Maschine.
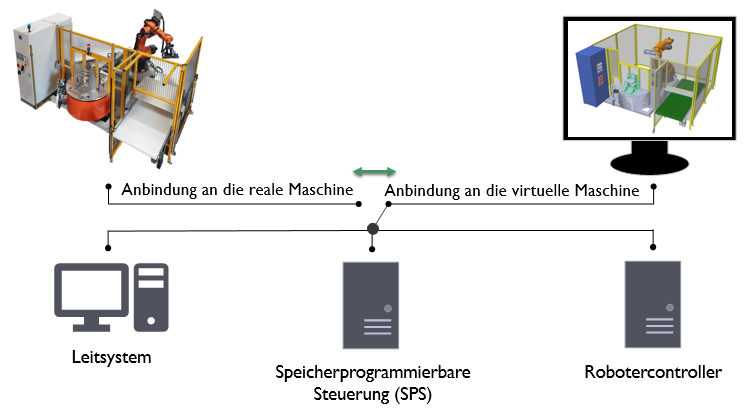
Abbildung 2: Der digitale Zwilling kommuniziert mit den realen Steuerungen. Die Steuerungen erkennen dabei keinen Unterschied zum realen Pendant. Im Anschluss an die virtuelle Inbetriebnahme am digitalen Zwilling werden die Steuerungen mit unverändertem Code an die reale Maschine angeschlossen.
twin bietet neben der Kopplung von Steuerungen unterschiedlichster Hersteller auch die Möglichkeit, physikbasiert zu simulieren. Damit kann das gesamte Verhalten der Maschine, inklusive Materialtransport, realistisch abgebildet werden.
Der Steuerungstechniker ist damit in der Lage, seine Software während des gesamten Bestellprozesses der Materialien, dem Zusammenbau der Mechanik und der anschließenden elektrischen Verkabelungen, vollständig zu testen. Und das ohne reale Maschine und ohne Mehraufwand – im Gegenteil, er hat zu jedem Zeitpunkt eine realistische und zudem auch visuelle Rückmeldung auf seine programmierten Codezeilen. Die gesamte, virtuelle Anlage, inklusive physikalischem Verhalten, befindet sich seit Projektstart auf dem Schreibtisch des Technikers.
Der digitale Zwilling, der in Abbildung 1 dargestellten Maschine, ist im nachfolgenden Videoclip, der Abbildung 3, ersichtlich. Gesteuert wird der Zwilling der späteren Produktionsmaschine, wie beschrieben, von den realen Steuerungen. Im Video sind zwei koordinierte Fahrwagen ersichtlich, die Materialien auf einen Arbeitsplatz befördern bzw. von diesem zu verschiedenen Ausgabestationen transportieren, nach dem ein Roboter einen Arbeitsprozess durchgeführt hat.
Abbildung 3: Der Steuerungscode wurde mit den realen Steuerungen an der virtuellen Maschine getestet und optimiert. Zwei Schlitten transportieren Materialien, die von einem Roboter bearbeitet werden. Der Materialtransport ist dank der physikbasierten Simulation in twin möglich.
Jene Zeit, die in dieser Phase des Projektes zur Optimierung des Steuerungscodes an der virtuellen Maschine investiert wird, wird später auf der Baustelle an der realen Maschine eingespart. Zum Zeitpunkt der Inbetriebnahme vor Ort werden dann die Steuerungssysteme mit der realen Maschine gekoppelt. Der Steuerungscode ist dann derselbe – nur vollständig getestet und optimiert!
Ein Ausschnitt des Automatikablaufs realen Inbetriebnahme der Produktionsmaschine ist in Abbildung 4 ersichtlich.
Abbildung 4: Die reale Maschine nach der erfolgreichen Inbetriebnahme. Die Inbetriebnahme Zeit konnte drastisch verkürzt werden, da der Steuerungscode bereits im Vorfeld ganzheitlich und umfangreich an der virtuellen Maschine mit twin getestet wurde.
„Steigende Komplexität, hohe Kundenansprüche und kurze verfügbare Inbetriebnahmezeiten im Sondermaschinenbau stellen uns tagtäglich vor Herausforderungen. Das Testen von Steuerungssoftware mit der Simulationsumgebung twin ermöglicht uns die Inbetriebnahme an der realen Maschine mit einem bereits im Vorfeld ausführlich und ganzheitlich getesteten Softwarestand durchzuführen. Das reduziert das Risiko an unvorhergesehen Fehlern im Produktionsbetrieb erheblich. Zudem verlagert sich die Zeit der Inbetriebnahme beim Kunden ins Engineering, was große Kosteneinsparungen mit sich bringt.“ – Martin Eberle, Geschäftsführer der Firma Eberle Automatische Systeme.
// Produkt
Virtuelle Inbetriebnahme mit der Simulationssoftware twin.
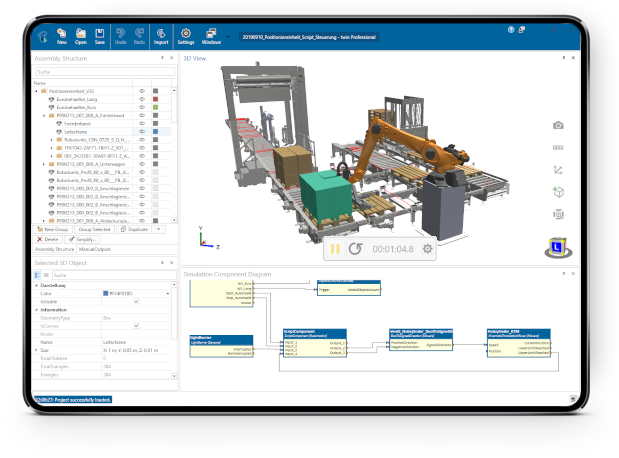