The Nesensohn small hydropower plant in Laterns
In the municipality of Laterns in Vorarlberg (Austria), this small hydroelectric power plant was built as early as 1922. Originally, the power plant was the only way to supply the village and surrounding farms with electricity. Today, Mr. Nesensohn operates this gem in the middle of the mountains and feeds the generated electricity into the public power grid. The small hydroelectric power plant is fed from an elevated reservoir, which in turn is supplied by two natural tributaries. The high reservoir is located at about 1.211m above sea level and the power plant itself at about 980m above sea level. The high reservoir and the power plant are connected by an underground pressure pipeline of about 977m total length. The plant has a generator with a nominal power of 50kW which is driven CO2-neutral by hydropower alone. Thus, such small hydropower plants are an important building block for the energy turnaround, climate protection and CO2-neutral power generation. About five years ago, the power plant was refurbished and the control technology was brought up to date. With this update, the power plant was also connected to the digifai control IoT platform, which supports the plant operator in operation and maintenance.
When there is a fire and the fire department goes out
In an emergency, when a fire needs to be extinguished, the water supply in the elevated reservoir is needed for firefighting water supply. For this purpose, a tapping point for extinguishing water is available about halfway along the power plant pressure line. In this situation, the power plant must shut down power production in a controlled manner and the elevated storage tank must supply the extraction point with sufficient water. The IoT platform supports the power plant operator in the emergency situation with automated alarm messages and location-independent access to the current operating states.
The IoT platform networks the widely distributed plant components
The power plant consists of several widely branched plant sections. The elevated reservoir is located about one kilometer from the power plant and has technical facilities such as level measurement, temperature measurement and discharge control by means of a gate valve. In addition, the elevated storage tank is monitored by a camera. The penstock must be monitored for pipe breakage and possible water loss over a length of approximately 977m to prevent damage from uncontrolled water leakage such as flooding or landslides. Furthermore, the extraction point for the extinguishing water must be monitored. If there is a demand for water withdrawal here, the power plant must be able to react in time. In the power plant itself, the technical equipment such as the generator, the bearing temperature, the flow rates and the operating parameters for power generation itself such as voltage, current, frequency, power, etc. must be monitored. Cameras are also available in the power plant itself to provide a remote view of the generator plant. An IoT platform offers the best conditions for linking the individual plant components. The necessary technologies for power plant monitoring such as the IoT interfaces for a wide variety of data sources, alarming functions, remote connections are available as standard. Due to the widely branched structure, it is a great advantage for the power plant operator to have mobile access to the individual plant components via the IoT platform.
Mobile monitoring facilitates power plant monitoring
Location-independent access to the current operating states of the power plant greatly facilitates power plant monitoring. With the IoT platform, all current and historical data as well as alarm and error messages can be viewed. No matter where the power plant operator is, the IoT platform and mobile monitoring give him access to the information he needs. Via the IoT platform, he can access all plant components while on the move. He gets an overview of the data of water resources, power production and directly via the IoT platform also the possibility to look remotely via the cameras into the individual parts of the plant. If there is a need for action, he could even actively intervene in the process via the IoT platform and control the plant components remotely.
Virtual data points replace costly measurement equipment
Extracting the necessary information from related data points and mapping it with virtual data points – this is possible with an IoT platform and the analysis tools implanted there as standard. In this case, the technology even replaces costly measuring equipment. Pipe burst monitoring at the Nesensohn power plant is monitored based on the outflowing water volume in the elevated reservoir and the incoming water volume at the power plant. The special feature in this plant is about halfway with the extraction point for fire water. The possible extraction of extinguishing water must of course be taken into account for this type of monitoring.Ultimately, however, it is data values which, considered in relation to each other, provide the necessary information as to whether the pipeline is intact. If the parameters do not match, an alarm message is generated immediately. The pipeline is monitored around the clock using virtually formed data points.
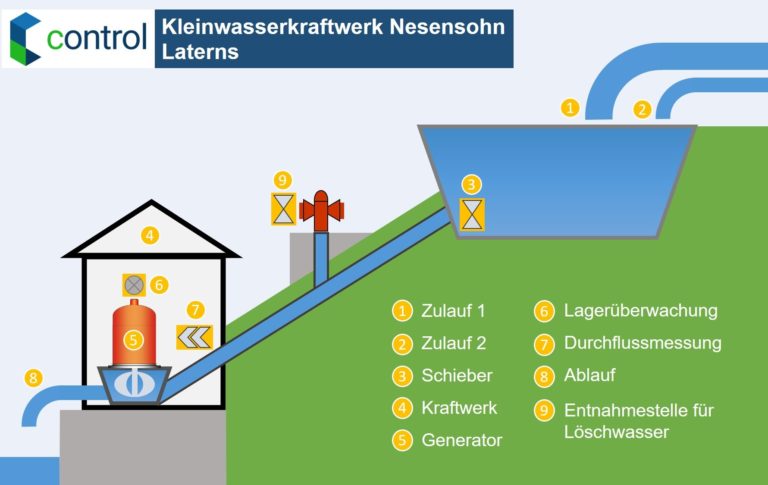
Picture 1: The picture shows the schematic connections of the small hydropower plant Nesensohn in Laterns. The turbine is fed from a pressure line from the high reservoir. In the event of an emergency, however, the elevated storage tank must give priority to supplying the extraction point for the extinguishing water.
Digital analysis tools for predictive maintenance
IoT platforms can collect data and gain information. Analysis tools are used to identify and determine trends and deviations. These functions are particularly important for predictive maintenance. These functions of the IoT platform are also in use at the Nesensohn power plant. One example is the bearing monitoring on the water wheel. The bearings are important components in the plant. A failure would mean a loss of production and a costly repair, as these are specially manufactured bearing shells. The IoT platform is used to monitor the storage temperature. The ambient temperature is also monitored. If the bearing temperature now rises in a ratio that is not typical of the ambient temperature, an error message and alarm is generated via the IoT platform. The power plant operator can now specifically investigate the cause and correct the fault in good time before the total failure. The IoT platform digitally supports the power plant operator in plant monitoring and is active around the clock.
Decentralized IoT networked energy supplies support in the energy transition
The use of alternative energy sources, such as hydropower in this example, or other alternative forms of energy generation, such as solar energy or plant-based energy sources, make an important contribution to the energy transition. The more such local decentralized energy supply sources emerge, the more important networking and the application of IoT technologies become. Only through networking and automated monitoring can such decentralized plants be operated economically and qualitatively in widely ramified plant networks. IoT platforms make alternative energy sources sustainable!
// Product
The IoT platform control for power plant monitoring.
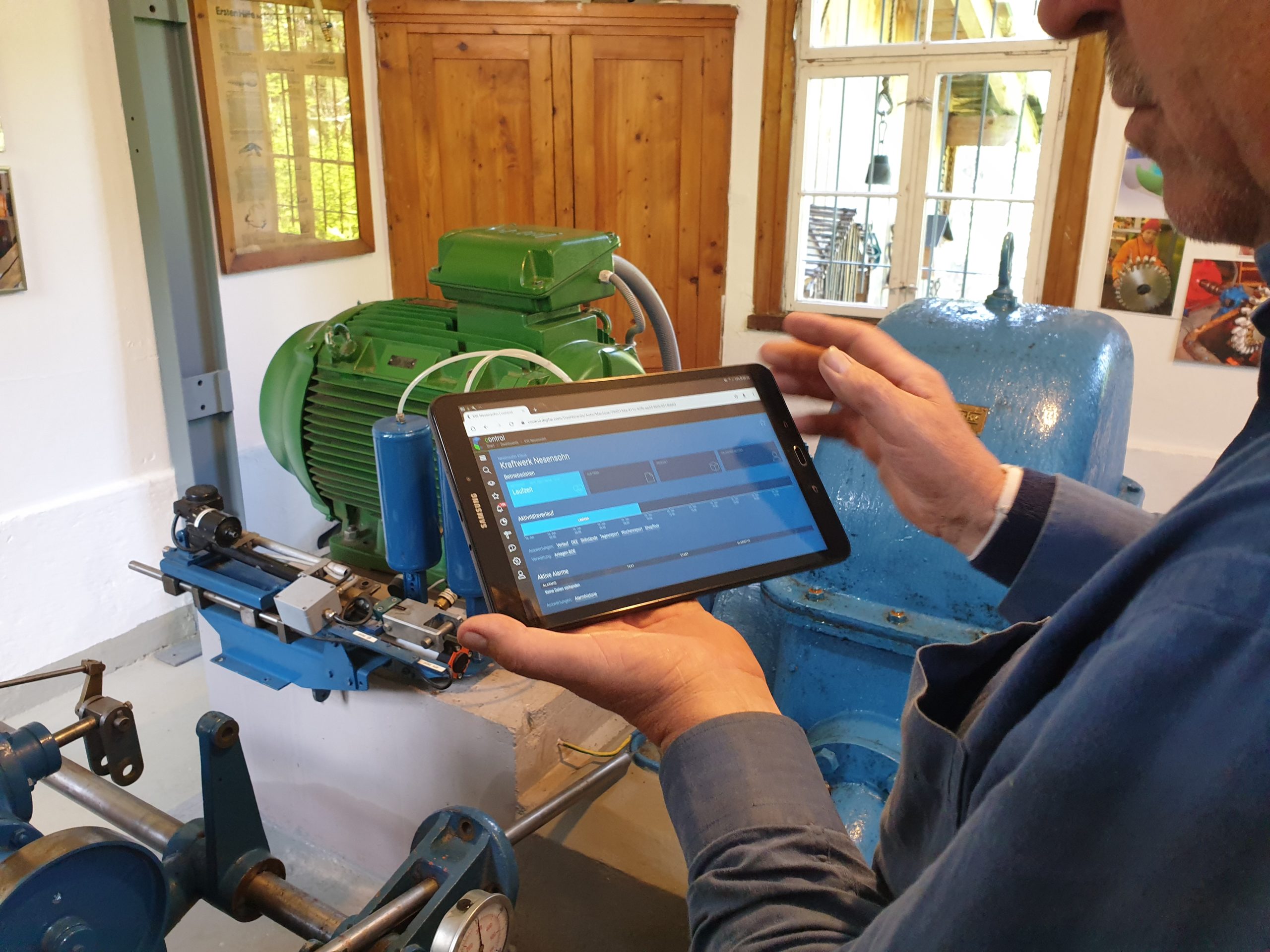