// winwin with twin
The leading all-round simulation software for machines and robots
Efficient, safe and cost-saving from idea to operation with twin.
// More Quality & Efficiency – Less Risk
Less risk and cost, greater efficiency and reliability – a real win-win. Simple and safe from the idea to operation with twin’s digital twin.
// References
Top companies develop with twin
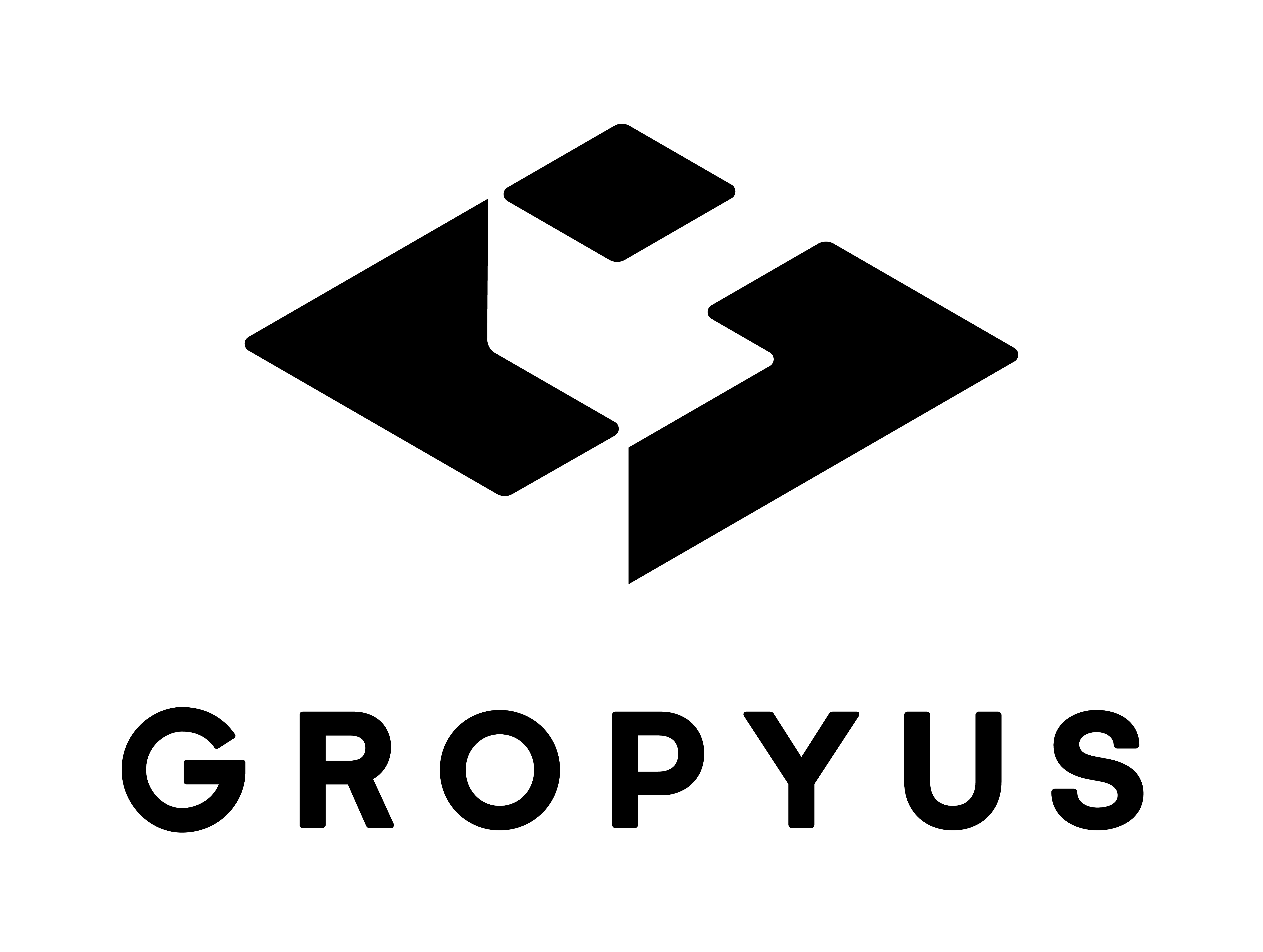
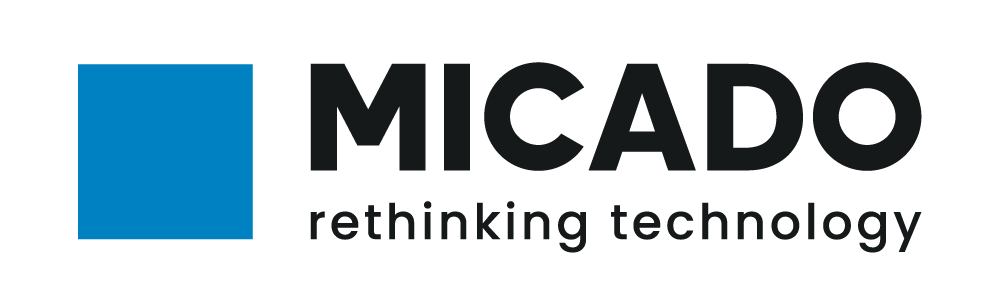

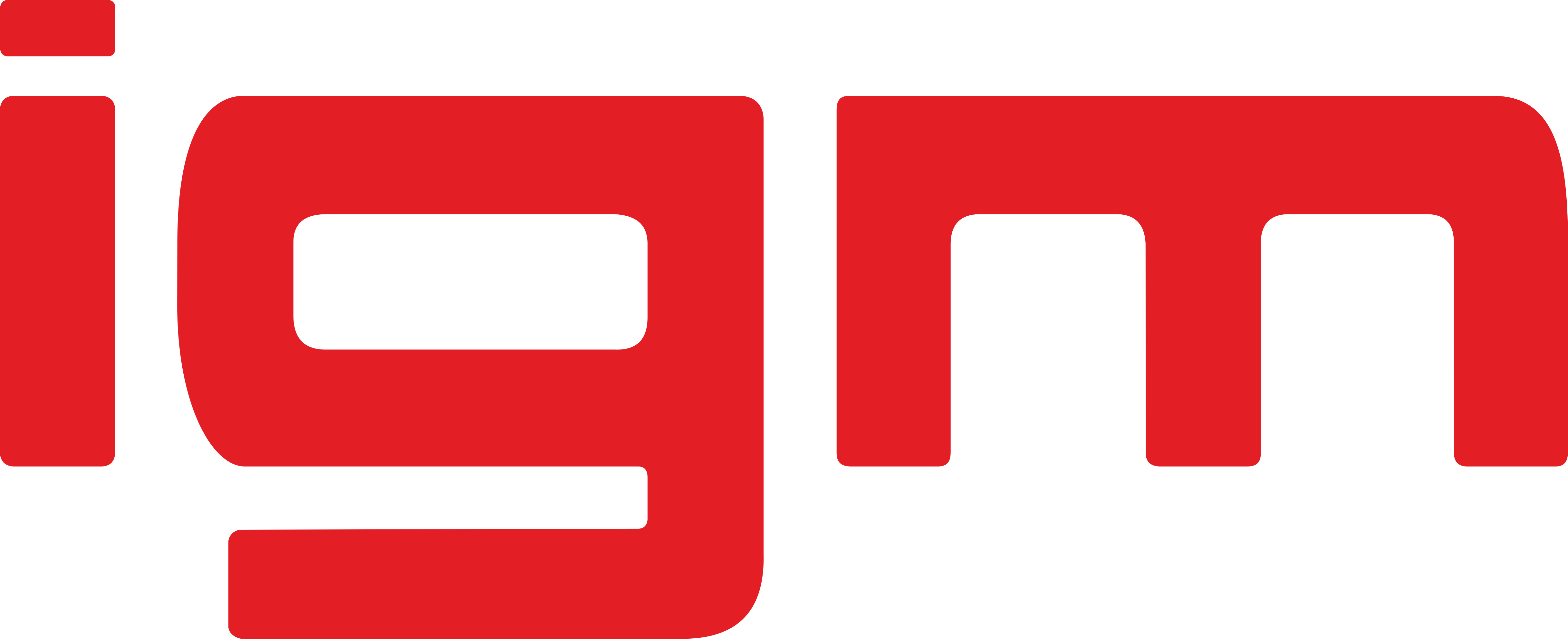
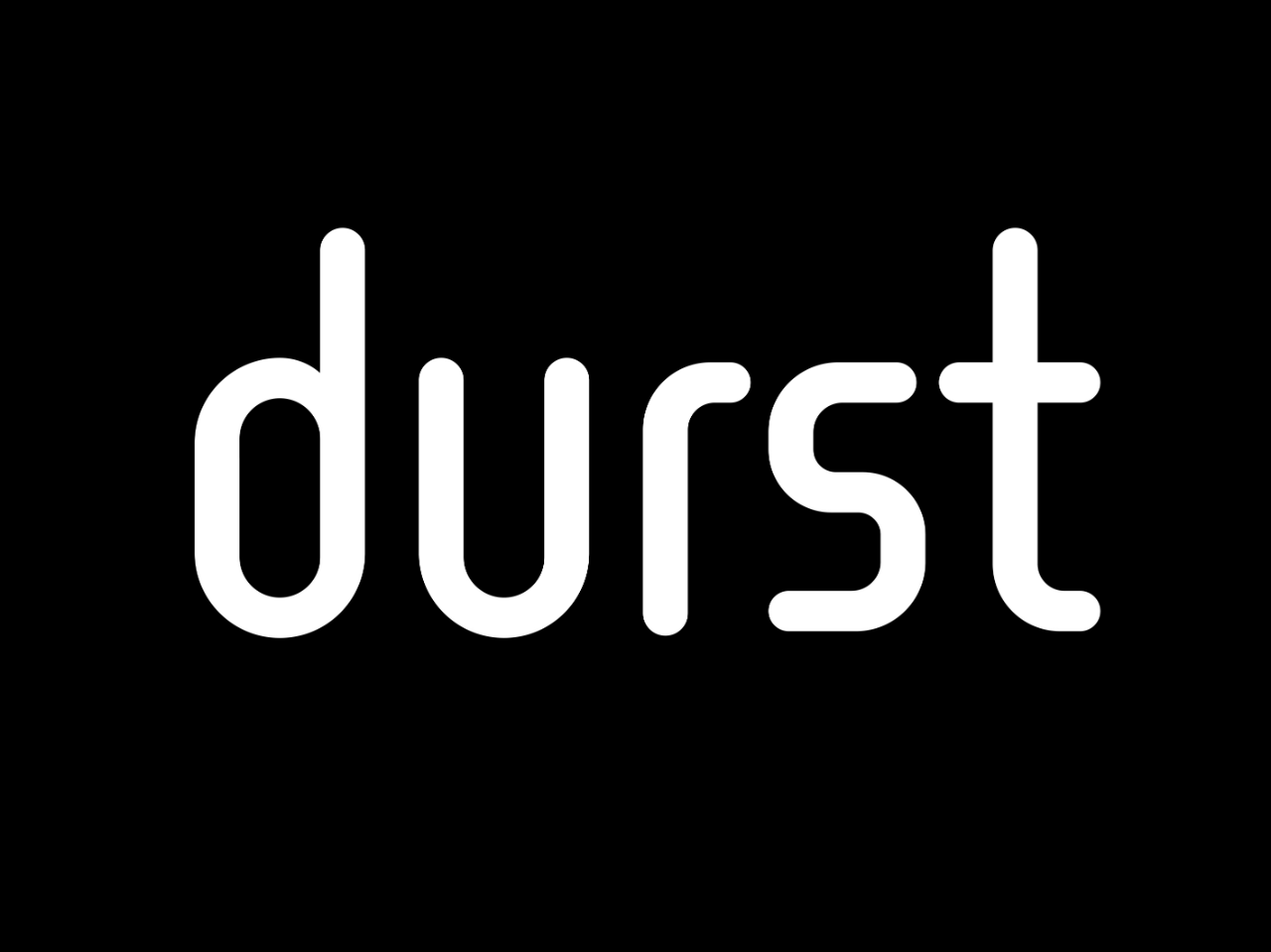
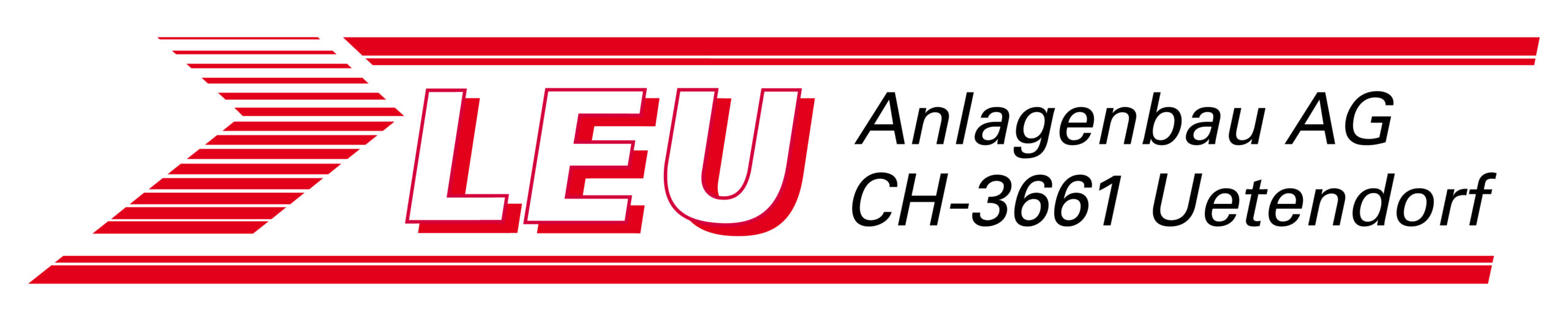
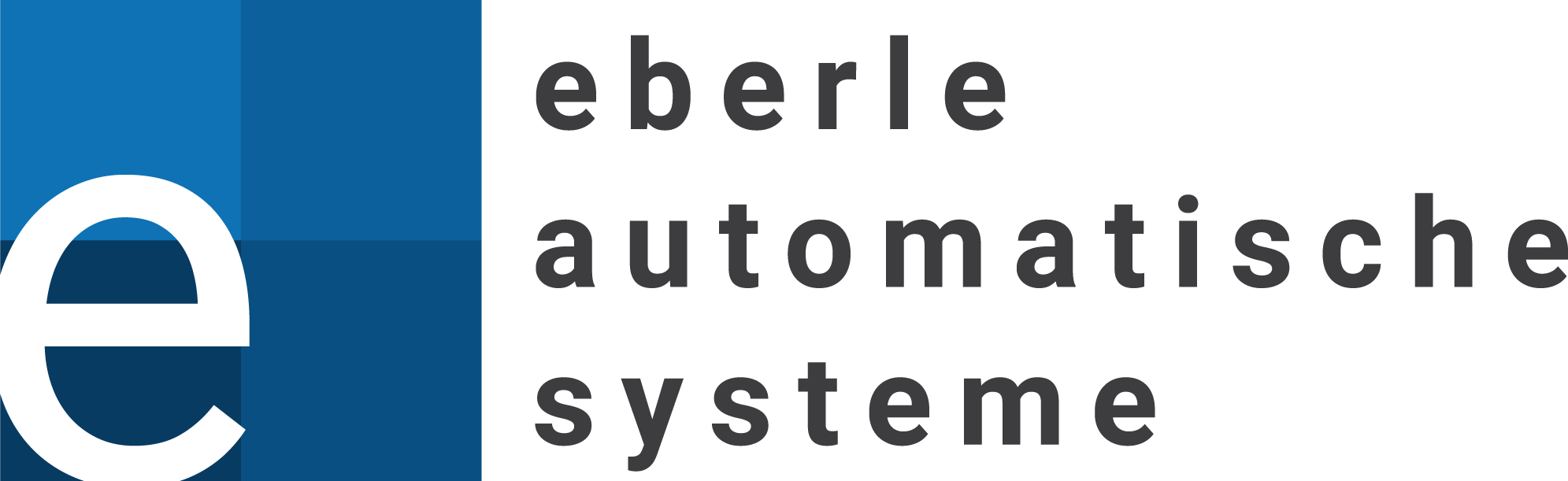
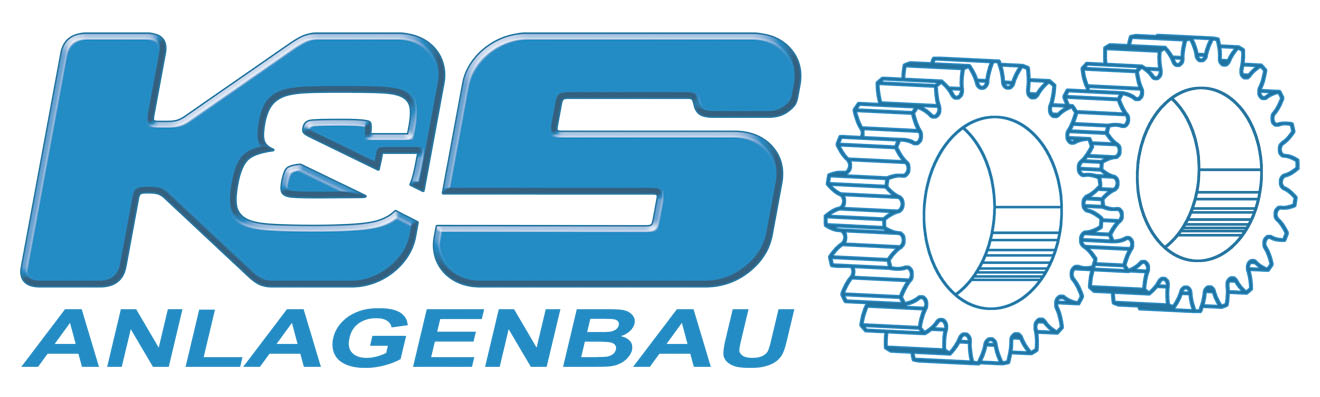
// In Sales
Start with digital feasibility studies
With twin, you can simulate realistic processes and scenarios right from the proposal stage. Inspire your customers and accelerate decision-making.
Simple creation of sequences
Create processes with drag-and-drop ease and without programming knowledge. By creating even complex processes with ease, you can identify design flaws and bottlenecks early on. This allows you to optimise your processes in no time at all.
Fast model creation thanks to library
Benefit from existing models and create your digital twin in a matter of seconds. Whether robots or your individual standards such as grippers or entire machine modules – with twin you can quickly integrate existing components and start your simulation in no time at all. Maximum flexibility, minimum effort – for faster results and more efficient workflows.
Real robot kinematics
Easily include robots in your concept simulations and optimise processes in no time. Easily create and optimise robot sequences directly in the simulation. With realistic speeds and accelerations, you can simulate movements accurately – for accurate cycle time estimates and optimised processes.
// In Engineering
Commission machines virtually
Put your machines into virtual operation before the real implementation begins. Speed up the development process and avoid costly errors.
Test your real control program
Test your real control program, robot program and HMI directly on the digital twin. Find and correct errors in your code before they cause real damage. Connecting a wide range of control systems to twin has never been easier, even with thousands of I/O signals.
Test and optimise mechanics
Check the functionality of your mechanical designs and optimise mechanical components directly in the simulation. twin’s state-of-the-art physics simulation realistically simulates forces and movements. This allows you to test and optimise even complex mechanical relationships.
Real-time collision detection
Identify and fix mechanical and software faults before real damage occurs. Save time and money with accurate simulations and early problem detection.
// In Operation
Intuitive 3D-HMI
Use advanced 3D HMIs that are not only intuitive, but also stunningly designed to improve machine usability.
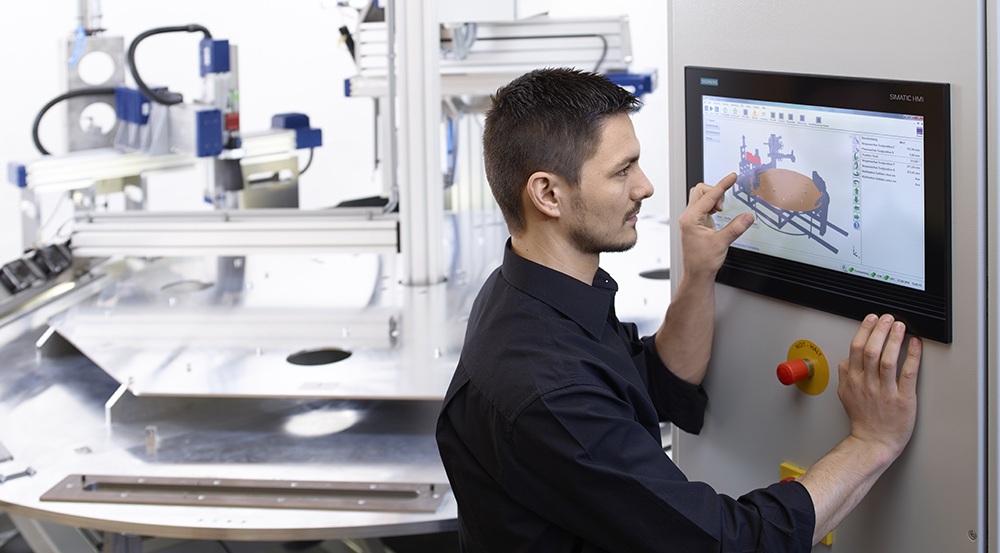
Seamless integration into existing HMIs
twin integrates seamlessly with existing HMI systems, regardless of vendor or architecture. This means you can use your familiar and proven environment and enhance it with the benefits of 3D operation.
Reuse models without additional effort
Save time and money by seamlessly reusing the models created in engineering in your HMIs. Added value without extra effort.
Improved user experience for plant operators
Provide a new user experience for the operator. This makes operation easier and reduces training costs and downtime. For example, display fault messages where they occur and guide operators through maintenance scenarios. Or enable natural operation where the operator can, for example, directly touch machine components in 3D to open manual operations.
// References
Our Customers’ Opinion
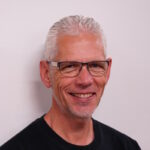
The simulation software twin delivers what digifai promises. We are thrilled.
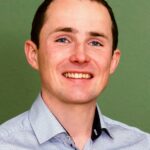
The software fulfils all our wishes – we can master even the most demanding requirements with twin. Such fast and competent support is unique. twin is constantly evolving and always focusses on customer needs. Keep up the good work!

We are an Austrian SME, develop turnkey special machines and have been looking for a suitable software for the virtual commissioning of our machines for a long time. With the software twin from digifai, we now secure the complete development process of our machines at an early stage and save valuable time during commissioning! With twin, we have definitely backed the right horse in this area!

twin offers us as a medium-sized special machine manufacturer the possibility to minimize risks in the concept phase, to secure the design at an early stage and with the virtual commissioning a shorter time-to-market for our customers.
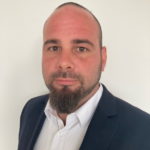
The possibility of simulating designs physically correctly, checking them for feasibility with various use cases and putting them into operation virtually opens up a completely new market access for us as a service provider in partnership with digifai.
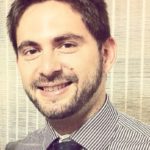
By simulating the entire machine at an early stage, we can significantly reduce risk and save costs. The entire control software including HMI and control system is ready and tested before the machine is built.

To conduct our research, we need a secure environment in which we can test AI algorithms for machines as realistically as possible. twin is perfectly suited for this purpose.

twin enables us to create digital twins of our production machines. digifai’s many years of experience as an integration partner is visible in the small but important details of their solutions.
// Therefore twin
Overview of the Available Features
By practitioners for practitioners: You will be amazed at how quickly you will find your way around the software.
You do not need a CAD program to work with twin. Easily import the most popular CAD formats.
Add sensors and actuators from an extensive library to your simulation.
Easily create sequences and behaviours with sequences and scripts.
Teach robot movements with the integrated robot controller.
Simple connection of controllers and robots even with thousands of signals.
Achieve unprecedented fidelity with state-of-the-art physics simulation. With minimal configuration.
Extend twin’s functionality to meet your needs.
At vero eos et accusam et justo duo dolores et ea rebum. Stet clita kasd gubergren, no sea takimata sanctus est
At vero eos et accusam et justo duo dolores et ea rebum. Stet clita kasd gubergren, no sea takimata sanctus est
I am text block. Click edit button to change this text. Lorem ipsum dolor sit amet, consectetur adipiscing elit. Ut elit tellus, luctus nec ullamcorper mattis, pulvinar dapibus leo.
I am text block. Click edit button to change this text. Lorem ipsum dolor sit amet, consectetur adipiscing elit. Ut elit tellus, luctus nec ullamcorper mattis, pulvinar dapibus leo.
I am text block. Click edit button to change this text. Lorem ipsum dolor sit amet, consectetur adipiscing elit. Ut elit tellus, luctus nec ullamcorper mattis, pulvinar dapibus leo.
I am text block. Click edit button to change this text. Lorem ipsum dolor sit amet, consectetur adipiscing elit. Ut elit tellus, luctus nec ullamcorper mattis, pulvinar dapibus leo.
I am text block. Click edit button to change this text. Lorem ipsum dolor sit amet, consectetur adipiscing elit. Ut elit tellus, luctus nec ullamcorper mattis, pulvinar dapibus leo.
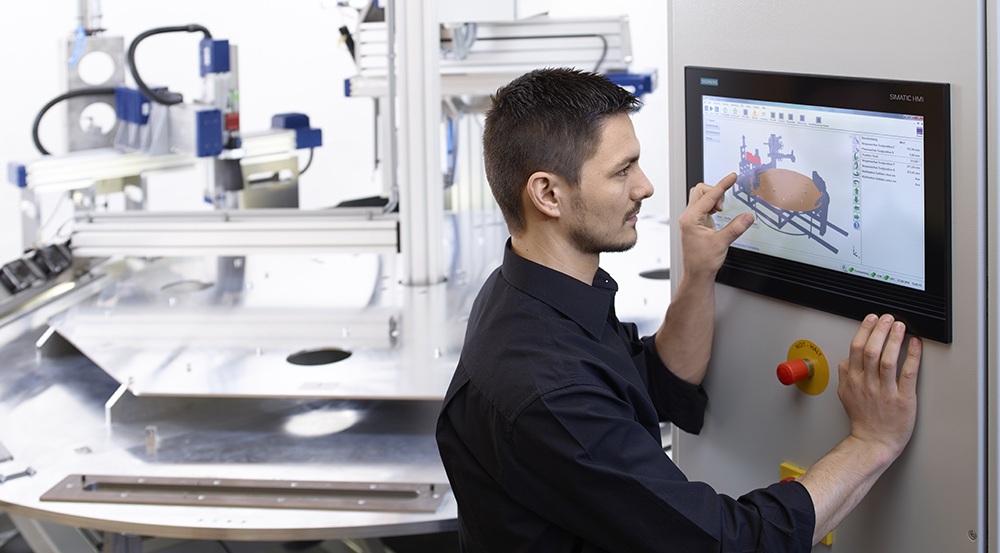
At vero eos et accusam et justo duo dolores et ea rebum. Stet clita kasd gubergren, no sea takimata sanctus est
At vero eos et accusam et justo duo dolores et ea rebum. Stet clita kasd gubergren, no sea takimata sanctus est
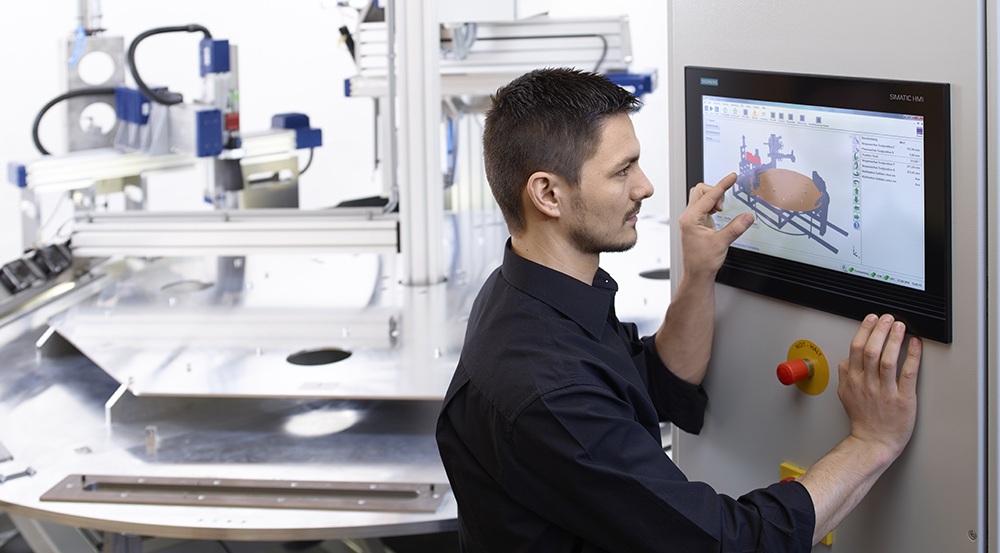
At vero eos et accusam et justo duo dolores et ea rebum. Stet clita kasd gubergren, no sea takimata sanctus est
At vero eos et accusam et justo duo dolores et ea rebum. Stet clita kasd gubergren, no sea takimata sanctus est
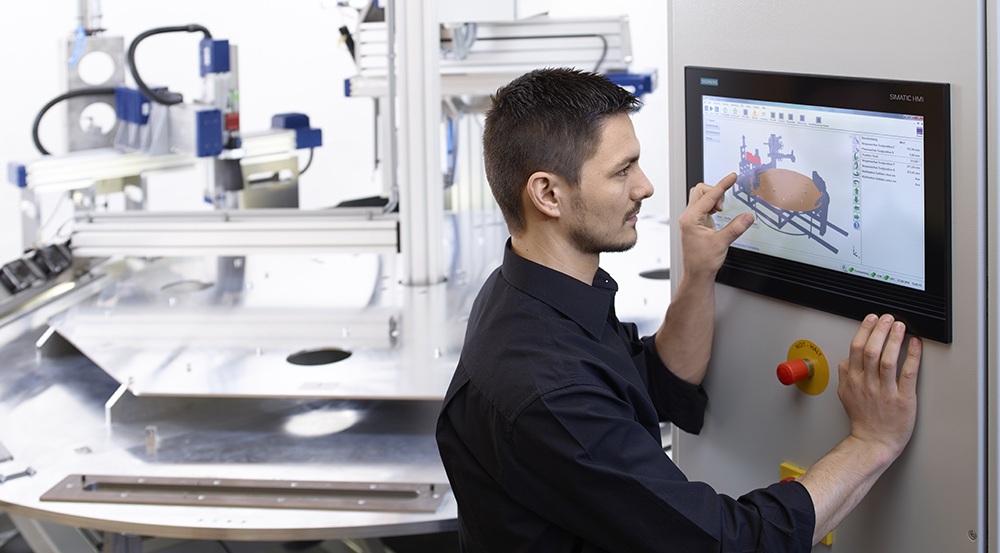
At vero eos et accusam et justo duo dolores et ea rebum. Stet clita kasd gubergren, no sea takimata sanctus est
At vero eos et accusam et justo duo dolores et ea rebum. Stet clita kasd gubergren, no sea takimata sanctus est
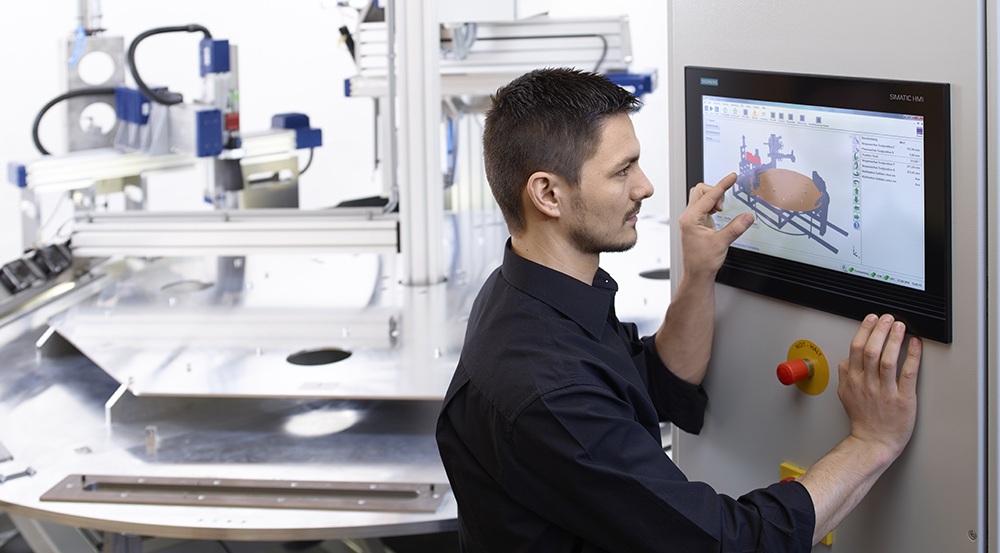
// More information on twin
Everything you need in one place
Whitepaper “Digital Twins in the Equipment Lifecycle”
A white paper on the use of digital twins in the plant life cycle (PDF file)
// More information on twin
FAQ’s
What sector is twin suitable for?
twin is a powerful all-round simulation software that is used in almost every industry. Whether automotive, food, woodworking, plastics, intralogistics or pharmaceuticals, twin offers flexible solutions for specific requirements. Benefit from software that allows you to optimise your processes across all industries.
Is twin suitable for special machines or standard machines?
Whether you are developing a special machine or a standard machine, twin is the right tool for the job. Our software reduces the risks in your machine building and automation projects, and its intuitive operation enables fast and reliable results.
Is there a free trial version?
Of course! You can request a free trial version of twin. This time-limited full version gives you the opportunity to test the full range of our software without obligation – experience the benefits of twin for yourself.
How do I learn to use twin?
Getting started with twin is easy: the software is clearly structured and intuitive to use. You can also benefit from a comprehensive range of training courses that will prepare you to use twin to its full potential right from the start.
Do I need a special computer to work with twin?
twin runs on all current computers and laptops. For optimum performance on particularly large or complex projects, we recommend a powerful system with a dedicated graphics card. This will ensure that your simulations run smoothly.
What licence models are available?
twin gives you maximum flexibility when it comes to licensing:
- Buy or rent: Decide for yourself whether you want to buy twin permanently or rent it flexibly.
- Individual licence types: Choose from a per-user licence, a per-computer licence or a network licence for maximum flexibility within your team.
Whatever your requirements, we can offer you a tailored solution that fits your business perfectly. Contact us and we will help you find the ideal licensing option.
How can I by twin?
Ready to get started with twin? Contact us directly by email – our team looks forward to working with you to find the best solution for your needs.
How often is the software updated?
We listen to our customers! That’s why every two months we release a new version of twin that takes your wishes and requirements into account. These regular updates ensure that you are always up to date – for maximum efficiency and innovation.
What can I do if I get stuck with a problem?
Our support team is here for you! Simply contact us by email or phone and one of our experts will help you quickly and competently. With twin, you are never alone.
Can I extend the software's functionality?
Yes, twin is modular and can be extended at will. With our Software Development Kit (SDK) you can develop your own modules – for example in C#. This allows you to tailor twin to your individual needs.
// Kontakt
Neugierig geworden?
Haben Sie ein konkretes Projekt vor Augen oder wollen Sie sich beraten lassen, ob Sie von digifai profitieren können? Ich freu mich auf Ihre Nachricht.
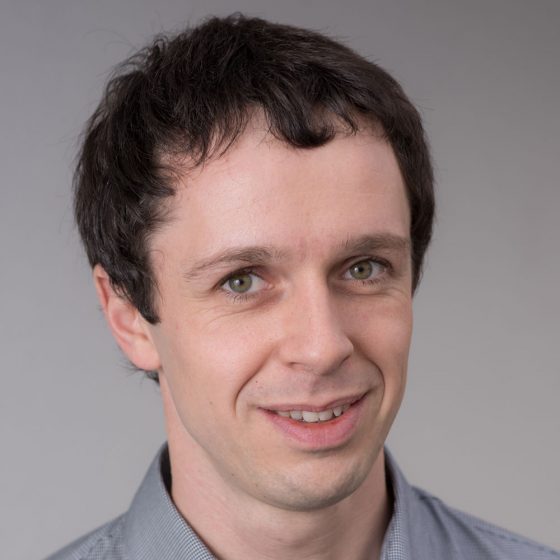
Michael Eberle
Chief Technology Officer
+43 5572 55580 803
michael.eberle@digifai.com